Foundry
A little of history
During early civilizations, metal production was dominated by more accessible alloys, such as bronze and copper. Aluminum, linked to other minerals, remains elusive. It was not until the 19th century that major advances made it possible to isolate aluminum from its natural components.
In 1825, Danish chemist Hans Christian Ørsted discovered the possibility of producing small quantities of aluminum by electrolysis. However, it would be several years before Frederick Wöhler, a German chemist, succeeded in producing aluminium in larger quantities using the sodium reduction process in 1845.
The watershed in the history of aluminum smelting survived in 1886, when Charles Martin Hall in the United-States and Paul Héroult in France, independently, developed a cryolite melt-based electrolysis process to extract aluminum. The aluminum on a large scale. This process, today called the Hall-Héroult process, remains the main method of producing aluminum.
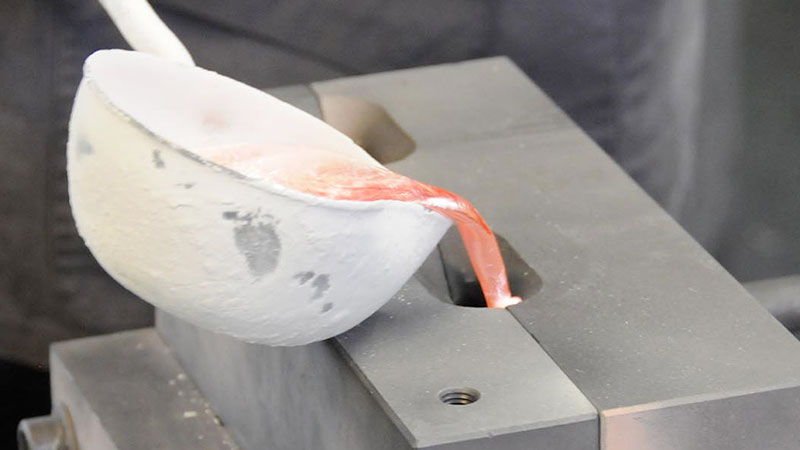
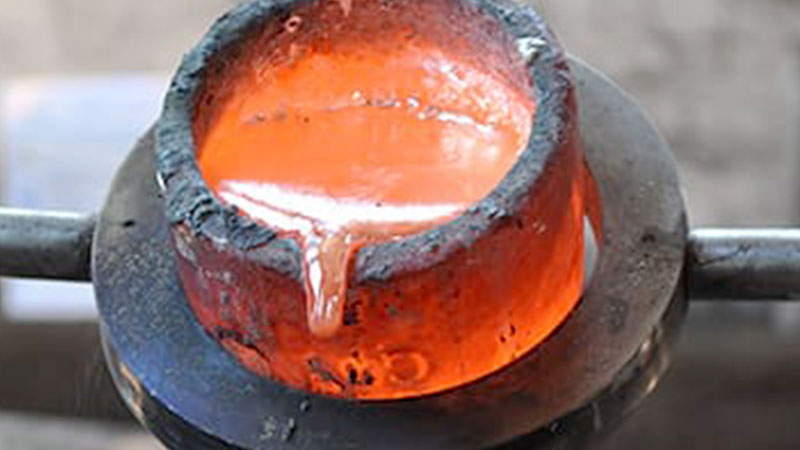
The foundry today
During the 20th century, significant progress was made to make aluminum production more efficient and economical. Innovations in kiln design, waste management and material purification were introduced. Aluminum smelting has also diversified to meet the growing needs of various industries, ranging from aerospace to automotive, packaging to electronics.
The advent of computing and digital modeling has revolutionized the design of aluminum parts, enabling increased precision and substantial material savings. Die casting, shell casting, and other modern techniques have emerged, providing specialized alternatives for specific applications.
Today, aluminum foundry is at the heart of many industries, playing a vital role in the manufacturing of critical components. Researchers are continually exploring new approaches, innovative alloys and more environmentally friendly methods to shape the future of aluminum foundry.From chance discovery to mass production, the evolution of aluminum foundry is a reflection of constant human ingenuity, marking a hsitory rich in technological progress.
Gravity
Gravity Die Casting consists of obtaining a part from a metal mold also called a shell or tool, into which a metal in the liquid state has been poured. The filling is carried out under the sole action of gravity, hence the name gravity shell molding.
Fond’AL tech Services supports you in the development of this process thanks to its experience in this field. From pre-study to final delivery to the customer, from the simplest to the most complex parts, we will be able to offer you the best solutions.
Low pressure
Low pressure die casting consists of vertically injecting, at low speed, the liquid metal from an oven placed under the mold via a ceramic tube (or poteyé cast iron) via a pressure of a neutral gas which, applied to the liquid metal, will force it to rise in the tube and fill the impression.
Fond’AL tech services, thanks to its experience in this process, will be able to demonstrate to you the strengths that low pressure can bring to the manufacturing of your parts. We support you from pre-study to final delivery.
We will also be able to find you the best solutions in the choice of equipment for the implementation of low pressure in your future investment projects.